Until recently, craft brewers worldwide purchased all their carbon dioxide (CO2) – rather than collecting it from fermentation as all large brewers do – because of low CO2 costs and the fact that small-scale CO2 liquification systems were not available. However, in recent years, the cost of CO2 has increased and supplies have been interrupted. This has resulted in a serious interest in CO2 collection and, as a result, a self-sustaining CO2 supply has been developed. Companies such as DALUM Beverage Equipment have scaled large brewery technology into CO2 collection plants that are sized for craft brewers specifically.
DALUM’s experience with selling CO2 plants around the world for about four years has allowed the company to define seven steps required for a successful CO2 collection project.
Determining a brewery’s “endgame”
The first step toward successful CO2 collection is to determine a brewery’s “endgame,” as in, what the brewery wants to accomplish. Typically, it is one (or a combination) of the following:
- Environmental concerns: The desire to minimize their carbon footprint. Owners see it as their duty and social responsibility to do what they can to improve the environment and may also see it as a marketing benefit.
- Cost reduction: Their CO2 costs have risen and continue to rise, and they are looking to reduce costs. If they can ultimately become CO2 self-sufficient, that is all the better.
- Ensuring supply and becoming CO2 self-sufficient: These brewers may have had difficulties getting CO2, which resulted in curtailing their production or being unable supply product to their consumers. To them, investment in becoming self-sufficient is “the cost of doing business.” Also, they can utilize all of the environmental and marketing advantages that come along with being CO2 self-sufficient.
Understanding a brewery’s collection potential
Based on brewing specifics such as original gravity, barrels per brew, brews per day, etc., a brewery must predict the CO2 generation rates to select the correct size of CO2 plant. A knowledgeable equipment supplier should be able to assist a brewery with modeling their brewing schedule. Special attention must be given to predicting the fermentation peaks, which will be used in properly sizing the collection plant.
Understanding a brewery’s current usage and consumption
To understand a brewery’s current usage and consumption, the brewery’s history and how many kilograms of CO2 are purchased per month, per year must be accurate. Are the deliveries based on actual usage or on how often the delivery truck is in the brewery’s area? Also, is the capacity of the brewery’s current liquid tank based on the brewery’s usage or how often it can get deliveries?
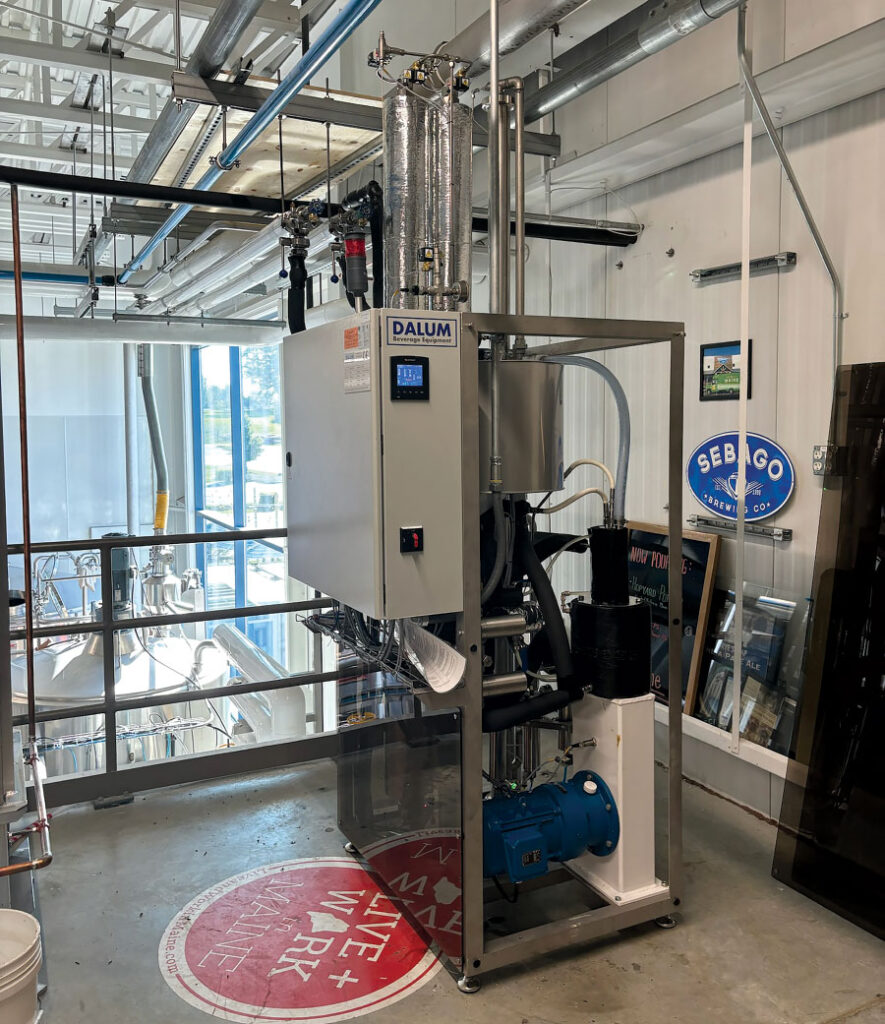
Determining a brewery’s peak CO2 gas flow rate will be used to size a vaporizer. Often, the current peak flow can be reduced by restricting the flow on non-time sensitive flows. For example, the flowrate when purging a tank can be excessive, but can be drastically reduced by controlling the flow, even if it takes a little bit longer.
Select the CO2 liquification plant
As craft CO2 collection is a relatively new concept, there are a very limited number of viable equipment suppliers. Brewers should consider all suppliers and carefully review the pros and cons of each. The most valuable tools for a buyer are references or even visiting an operating installation and discussing it with another brewer in person.
Determine first-hand if the equipment will meet the brewery’s endgame. If a brewery wants to be self-sufficient, is the plant reliable? How much downtime have they experienced, and how was the factory support and service? What are the operating costs for consumables, time between overhauls, etc.?
When a brewery is collecting and using gas from its own product rather than purchasing from an unknown source, it assures the product will be free of any outside contaminants. However, it is important to select a plant that is guaranteed to liquefy the gas collected from fermenters to meet food-grade or beverage grade CO2 standards. The gas from the collected liquid should be, at a minimum, 99.9 per cent pure and absolutely free of any odors.
After the fermentation starts, the yeast takes no days off. Fermentation is a 24 hour a day, seven day a week process, and the collection plant must be designed to run continuously, start and stop automatically and provide alarms to key personnel via text messages. Remote monitoring of the CO2 plant during brewery off-hours via a mobile app should also be part of the system.
Select the storage tank and vaporizer
The storage tank is the number one dilemma facing craft brewers. Most craft brewers lease their existing tanks and vaporizers, and for a valid reason: Their CO2 suppliers will not allow them to push their collected liquid into the tank. As mentioned above, the size of the existing tank is based on both usage and the delivery schedule. If a brewery wants to be self-sufficient, the tank would be sized based on the collection rate and the usage rate with a buffer in-between to balance the two. It may be an option to purchase the existing leased tank, however, brewers are urged to do a thorough evaluation of the tank.
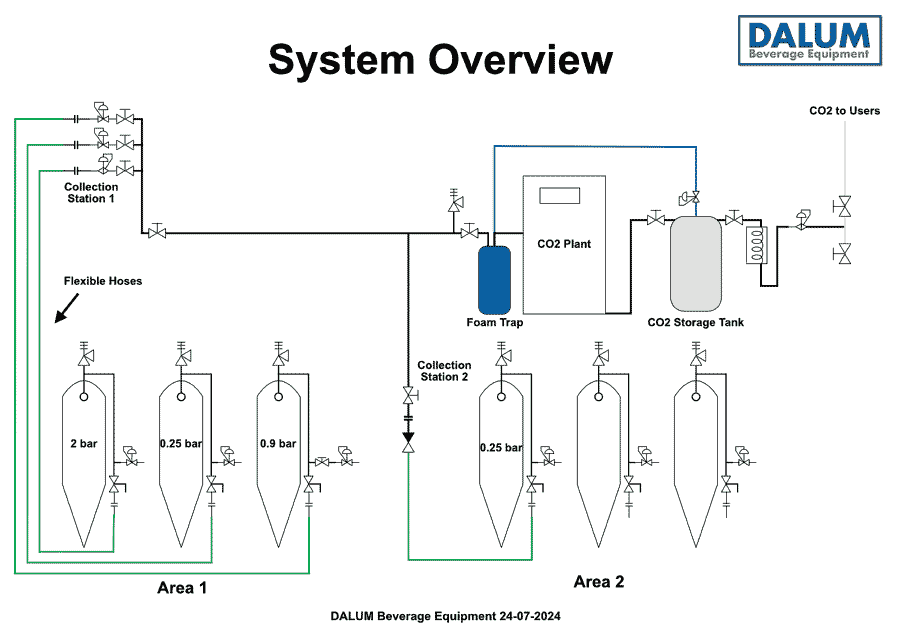
Used tanks can have failing insulation or other maintenance issues, which are expensive to correct. It may also be an option to continue leasing an existing tank without future CO2 purchases. New tanks often offer superior insulation and coating systems, which will minimize ongoing operating and maintenance costs. In most cases, the vaporizer is also leased with the tank. Most leased vaporizers are electric, as they are compact and usually mounted adjacent to the tank, but they are the most expensive to operate. Breweries should consider atmospheric vaporizers if space and climate are favourable.
Gas collection system
As CO2 collection was never envisioned, craft breweries practically have none of the piping infrastructure required to collect gas from the fermenters to a central liquification plant. Generally, it is best to place the plant as close to the gas source as possible, as this will minimize piping lengths and pipe diameters.
Collection piping can be simple and inexpensive, sophisticated and expensive or somewhere in-between. The best advice is for buyers to get references from their customers and to visit an installation. Brewers should inspect for themselves and determine what they need for their facility.
All plants will require a foam-trap before the unit. This small vessel of about two barrels in capacity is not designed to handle heavy foaming conditions, but as a last line of defense to prevent any liquid from entering the compressor.
Start-up and operation
The two most common operational issues that will greatly impact the performance of the collection system (as in, reduce the amount of gas collected) are:
- Tanks must be connected to the CO2 collection plant after the CO2 purity reaches an acceptable level as determined by the equipment supplier. After the fermenter is full, the fermentation will start, and CO2 will begin to push the air out from the headspace above the wort. After some time, usually hours after the fermenter is full, the gas will be pure enough to collect. Failure to do this will result in the loss of the gas at a time when fermentation is very vigorous. Large breweries use automatic valves and systems to place fermenters on collect. This can be too costly for craft breweries, so some will set up manual systems, where a schedule is kept and tanks are connected manually. DALUM has developed an automatic system, which will be offered in late 2024.
- Foaming will make it impossible to collect gas from that fermenter. When over-foaming occurs, the gas cannot be pushed through the collection piping to the foam trap and the gas from that entire fermenter will be lost. Foaming must be avoided, and there are some subtle process changes that can be utilized to accomplish this without affecting the final product.
CO2 collection is commonplace in large breweries and is now becoming feasible in craft breweries. As some breweries were never designed with CO2 collection in mind, and few craft brewers have experience with it, CO2 collection can initially seem overwhelming. However, when taken piece by piece, and step by step, collection and liquification is actually a simple process – less complicated than brewing a quality beer!
John Kiedrowski is managing director of DALUM USA and chairman of DALUM Beverage Equipment ApS, Denmark. Kiedrowski has a degree in mechanical and industrial engineering from the University of Wisconsin-Milwaukee and is a licensed professional engineer in Wisconsin. He was employed with Miller Brewing Company for 24 years, working in brewery operations and brewery engineering, and overseeing projects at Miller’s craft breweries. He was also the director of engineering at Cervecería Nacional Dominicana for eight years, directing expansions at their two breweries in the Dominican Republic. He can be reached at john@dalumequipment.com.